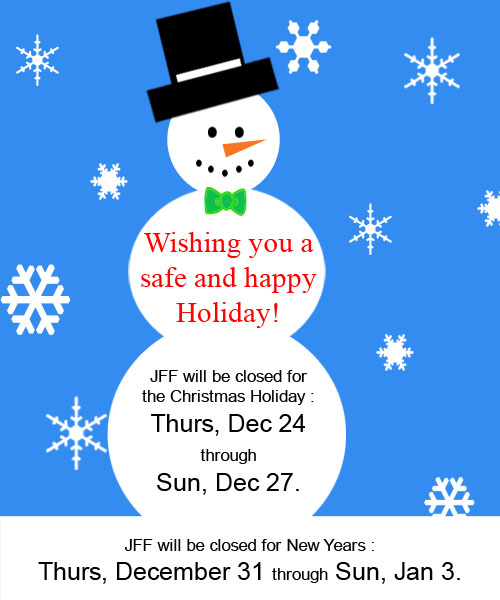
go back to JFF
22 December 2009
11 December 2009
Archives August 2008 : Tool of the Month
Tool of the Month : Drawplate
I recently began an apprenticeship with a local jeweler and goldsmith and have been working with many tools I never thought I would ever touch, except maybe to unpack from a box and place on a shelf. A few weeks ago, I was asked to draw down some gold wire using a draw plate. Typically, the suggestion of using a draw plate immediately would stir a reaction of disgust and plain laziness. "Why in the world would I need to draw down my wire, when I can just buy it in the gauge I need?!" I decided to keep an open mind and try it as I was curious to see how difficult it REALLY was. I annealed the wire, filed a point on one end and started pulling the wire through the draw plate. It was a breeze, and, I can't believe I'm saying this, fun!
A drawplate is a bar of hardened steel with holes of decreasing size. Each hole is shaped like a funnel, having the larger opening at the back end. Typically a drawplate will have 20 to 30 holes with sizes ranging within a 2 to 3 millimeter span. A draw plate is used in conjunction with heavy duty pliers called draw tongs that have a coarse jaw and a curved handle for a strong grip.
Draw plates are extremely versatile. They are typically used for reducing round wire to the size you need, but they also:
- reduce the outside diameter of tubing (this also makes the tubing walls thicker, which can be especially advantageous in tube setting).
- aid in making head pins and rivets.
- draw round wire into square or any other shape you can imagine (this also works for tubing).
Draw plates are available in a multitude of shapes. The most common shape is round, however; JFF also carries square and half-round. We can special order drawplates in other shapes as well.
The quality and price of drawplates vary drastically. The best quality drawplate is made of hardened steel and has A quality tungsten carbide inserts in the holes. The A quality tungsten carbide has a high polish finish and leaves the wire shiny and smooth after each pass through the draw plate, however; a tungsten carbide draw plate is expensive (upwards of $120). Be careful when purchasing tungsten carbide draw plates, as there are many imitators with more attractive price tags. These are not finished to a high polish and have pits and will cause unwanted problems.
A hardened tool steel draw plate is also a good choice, but after the drawing process, the wire is usually dull. It is also more difficult to draw the wire through the plate than the aforementioned tungsten draw plate. The tool steel drawplates range in price from $50 to $100.
Steel draw plates that have not been hardened, or are not tool steel, are not recommended for reducing the size of wire, because the hole will actually deform during the drawing process. They are, however; excellent for making head pins and rivets. These steel draw plates are priced around $15.
Archives July 2008 : Question & Answers
Q: Why are the measurements on a ring mandrel different than a finger sizer?
A: Ring mandrels are typically engraved with the sizes and then hardened. The hardening process causes the steel to expand and shrink along the mandrel, so that the engraved sizes are no longer 100% accurate. Unfortunately, the engraving cannot occur after the hardening process. And if the ring mandrel is not hardened, any hammering that occurs on it will change the shape and size of the mandrel as well.
To deal with this problem, it is always best to have a finger sizer along with a ring mandrel and check the sizes on your ring mandrel with your finger sizer for comparison.
A: Ring mandrels are typically engraved with the sizes and then hardened. The hardening process causes the steel to expand and shrink along the mandrel, so that the engraved sizes are no longer 100% accurate. Unfortunately, the engraving cannot occur after the hardening process. And if the ring mandrel is not hardened, any hammering that occurs on it will change the shape and size of the mandrel as well.
To deal with this problem, it is always best to have a finger sizer along with a ring mandrel and check the sizes on your ring mandrel with your finger sizer for comparison.
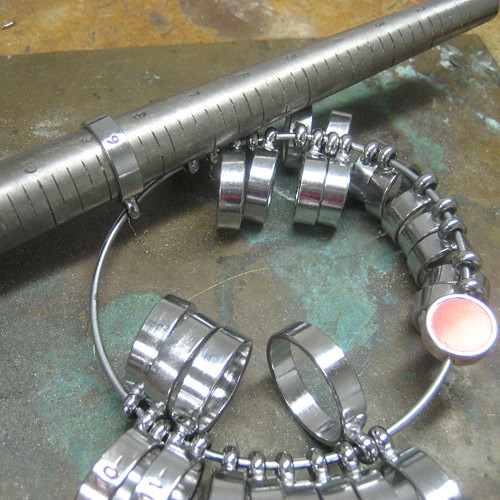
Archives July 2008 : Jeweler of the Month
Jeweler of the Month :
Judy Parady
Judy Parady
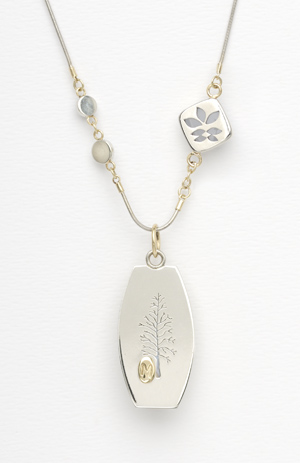
When I was in high school, I worked in a Buckhead boutique that sold rock and roll clothing, hash pipes, and lots of hippie jewelry

My Bachelor of Visual Arts degree from Georgia State University is in Jewelry Design and Silversmithing where I studied with Jem Freyaldenhoven and Richard Mafong. I've studied with other notables in the art world, but after all these years I've discarded almost all of their influences, except for the passion.
I make art in other mediums, too - sculpture, paintings, and drawings.
What was your first piece?
My first finished piece of jewelry, which I still have, was a big, gloppy cast ring featuring a really ugly teal green and orange agate. In retrospect, I don't think the teacher at the community art center knew very much about jewelry making or design. He showed us how to make wax models using soft brown sculptor's wax. There was no way to control the detail or scale. Somehow, that experience did not deter me from further exploration.
Who are your jewelry heroes?
In college, I related very closely to Jem Freyaldenhoven. His primary influence was for quality craftsmanship and personal, authentic design. I miss him still.

What is your design inspiration?
The mother of desing is always nature. I especially look at plants for texture, color, form and proportion.
What is your favorite part of making jewelry?
My favorite part of making jewelry is wearing it. Women jewelers definitely have an advantage when it comes to "test driving" new designs.
I also very much enjoy teaching jewelry making. So much so that I hold classes in my studio.
What is on your bench now?
I have a couple custom jobs - wedding things, and a big moonstone ring. But, I am most excited about new opportunities to place my jewelry in galleries and stores.

I just shipped a dozen pieces to a great jewelry gallery in Seattle and am currently preparing for work in the Signature Shop here in Atlanta.
What is your most indispensible tool?
Sadly, it is in my Optivisors.
My most beloved tool is a little brass ruler from the old Jewelers Supply Co that was located in downtown while I was in college.
I know there are massive changes in the industry with CadCam devices, laser welders, and the like. However, for the studio jeweler I think the biggest improvements are in finishing products like the bristle wheels from 3M. They remove oxides, while preserving texture and detail.
Labels:
archives,
Jeweler of the Month,
newsletter
09 December 2009
Archives July 2008 : Tool of the Month
Teborg Round Nose Pliers
Lindstrom pliers have long been the nicest and best round nose pliers to own. If you didn't already have a pair, they were on your wish list. Not only because of their small size, but also because they were made of premium Swedish steel and were hand finished to perfection. Even though these features did not come cheap, nothing compared.
Recently, Lindstrom was bought out and is now being manufactured in France and Spain. The pliers are also being made with a lap joint, instead of the stronger, more durable, box joint. And, to top it off the price has INCREASED!! The changes in finishing and size were also surprising.
We are sad to see a company with such a wonderful reputation as Lindstrom find it necessary to lower their quality to stay competitive; however, with these changes, Hans wanted to find a replacement for the Linstrom quality.
Teborg Pliers! They are manufactured in Sweden and are made out of Swedish steel. They are hand finished and are as small, if not smaller than the original Lindstrom round nose pliers. The tip of the pliers measure .7mm and gradually increases to the base, measuring 4.5mm. The length of the nose is 19mm. The finishing of the pliers is immaculate and feels similar to that of the original Lindstrom pliers, but they do not have the price tag of the Lindstrom pliers.

08 December 2009
Archives June 2008 : Tool of the Month
Artifex Wheel
Most people can barely walk out of the door without Dallas suggesting a tool that will and does make your project or life easier. The Artifex wheel is one of those tools that ALL of us (Hans included) are sold on!
The Artifex wheel is a German-made, rubber and silicon carbide bonded wheel. It will grind and de-bur very quickly, while it leaves behind a smooth, matte finish. Artifex wheels are bonded so they will not grind away into nothing and do not create a lot of dust like most other silicone based wheels. The Artifex wheel works great on silver, gold, platinum, and even steel!
The wheels are available in three different grits: Fine (250), Medium (150), and Coarse (80). However, we suggest using the Medium for most projects. The wheels are 4 inches in diameter and will fit on most polishing motors. They are also available on an inside ring arbor, in the Fine and Medium grits only. Artifex wheels are not available for the flext-shaft as of yet, but here's hoping!

Subscribe to:
Posts (Atom)