A: The quick and easy answer is “yes.” But as many of you know, the question and answer section is never a cut and dry answer.
Let me begin by explaining what gold-filled is. Like many of our tools in jewelry making the name is misleading, gold filled is not “filled with gold.” It is a thin layer of gold filled with a core of another less expensive material. Usually a copper-rich material like brass or bronze. The layer of gold is attached to the base metal core through a process called alloy diffusion. Allowing for a much thicker layer of gold than plating can produce.
Alloy diffusion begins with quickly heating and welding the two metals in a high heat furnace and then removing and immediately pressing the composite in a hydraulic press. The process continues by rolling in a rolling mill. Combined with annealing, the welded bond between the gold layer and base metal is further enhanced. The resulting weld is so strong that the finished gold filled sheet stock can be formed, fabricated and soldered without any risk of delamination.
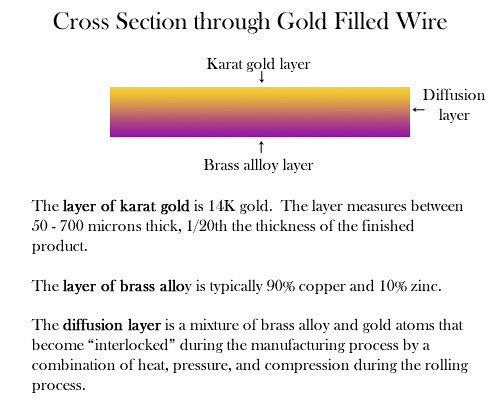
Now, back to the question at hand. Can you solder gold filled? Two big red flags cause a problem when soldering gold-filled: the copper-rich core and the thin layer of gold on the surface. When heated, the copper will raise to the surface, much like soldering silver. This causes a pinkish color after pickling, much like rose gold. Which is not a problem if you don’t mind the color, but if you want yellow gold, not good. The copper core also presents an increased risk of firescale. The first inclination to deal with firescale and/or the color change is to file, grind, and polish.
This is where the thin layer of gold on the surface creates the next hurdle. The surface does not have enough gold to with stand grinding away the firescale without taking all of the gold off with it. Thus leaving the brass or bronze core exposed, which will tarnish while the gold will not.
Ok, so how are you supposed to deal with these problems?
- Boric Acid and Denatured Alcohol Solution: dipping the pieces to be soldered in a saturated solution of boric acid and denatured alcohol is a traditional bench jeweler’s technique to prevent firescale on gold. By burning the alcohol off, a protective coat of boric acid is left all over the gold filled. Flux, solder and pickle as you would normally afterward.
- Charcoal Block: the charcoal block removes much of the oxygen from the flame which will decrease your chances of having firescale.
- Depletion Gilding: a process of heating to annealing temperature, pickling and brass brushing, and repeating 5-7 times. After soldering and pickling the piece, the process of depletion gilding will remove the pink color on the surface of the gold filled. However, this is a time intensive process and rather difficult when working on a link necklace.
- Use gold solder, preferably a 14K easy solder.
- Pick solder, thus controlling the amount of solder used and decrease the amount of solder clean-up needed.
- Solder quickly, the less time you heat the piece, the lower your chance of having firescale.
No comments:
Post a Comment